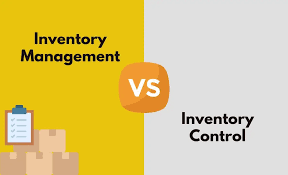
Introduction to Inventory Management And Inventory Control
Inventory management refers to the overall process of planning, procuring, storing, and controlling the inventory levels of goods in a business. It involves determining the optimal inventory levels, the ordering frequency, and the methods of storage, as well as forecasting demand and tracking inventory costs. Effective inventory management ensures that a business has the right amount of inventory at the right time to meet customer demand while minimizing inventory costs.
Inventory control, on the other hand, is a narrower concept that focuses on the monitoring and management of inventory levels within a business. It is the process of ensuring that inventory is properly counted, tracked, and accounted for. Inventory control involves maintaining accurate inventory records, identifying and addressing discrepancies, and implementing measures to prevent stockouts or overstocking.
The key difference between inventory management and inventory control is that inventory management is a broader concept that encompasses all activities related to inventory, while inventory control is a specific activity that falls under the umbrella of inventory management. Inventory control is a critical component of effective inventory management, as it helps businesses maintain accurate inventory records and optimize inventory levels to meet customer demand while minimizing inventory holding costs.
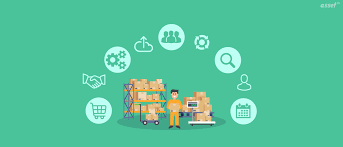
6 Differences between Inventory Management and Inventory Control with Table
Parameter | Inventory Management | Inventory Control |
---|---|---|
Definition | The overall process of planning, procuring, storing, and controlling inventory levels of goods in a business | The process of ensuring that inventory is properly counted, tracked, and accounted for |
Scope | Broad, encompassing all activities related to inventory | Narrow, focusing specifically on monitoring and managing inventory levels |
Objectives | Optimize inventory levels, minimize costs, and meet customer demand | Maintain accurate inventory records, prevent stockouts and overstocking |
Activities | Demand forecasting, inventory planning, procurement, storage, inventory tracking, cost analysis, risk management | Physical inventory counting, inventory recordkeeping, discrepancy identification and resolution, inventory replenishment |
Timeframe | Long-term, strategic planning | Short-term, day-to-day operations |
Metrics | Inventory turnover, carrying costs, stockouts, customer satisfaction | Inventory accuracy, shrinkage, stockouts, order fill rate |
Inventory management is a broader concept that encompasses all activities related to inventory planning and control, while inventory control is a specific activity that focuses on ensuring that inventory is accurately counted and accounted for to avoid stockouts or overstocking. Effective inventory management requires a combination of both activities, as well as careful monitoring of key metrics to optimize inventory levels, minimize costs, and meet customer demand.
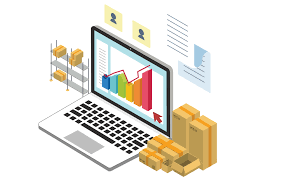
Point-Wise Differences Between Inventory Management and Inventory Control
Inventory Management:
- Refers to the overall process of planning, procuring, storing, and controlling inventory levels of goods in a business.
- Involves determining the optimal inventory levels, ordering frequency, methods of storage, and forecasting demand.
- It is a broader concept that encompasses all activities related to inventory, including demand forecasting, procurement, storage, inventory tracking, cost analysis, and risk management.
- Aims to optimize inventory levels, minimize costs, and meet customer demand.
- It is a long-term, strategic planning process that requires the involvement of various departments such as sales, production, and finance.
- Key metrics for measuring inventory management success include inventory turnover, carrying costs, stockouts, and customer satisfaction.
Inventory Control:
- Refers to the process of ensuring that inventory is properly counted, tracked, and accounted for.
- Involves maintaining accurate inventory records, identifying and addressing discrepancies, and implementing measures to prevent stockouts or overstocking.
- It is a narrower concept that focuses specifically on monitoring and managing inventory levels within a business.
- Aims to maintain accurate inventory records, prevent stockouts, and avoid overstocking.
- It is a short-term, day-to-day operations process that involves physical inventory counting, record-keeping, discrepancy identification, and inventory replenishment.
- Key metrics for measuring inventory control success include inventory accuracy, shrinkage, stockouts, and order fill rate.
Some Examples of Inventory Management and Inventory Control in Different Industries
Inventory Management:
- Retail: A retail store uses inventory management to ensure that it has the right amount of products in stock to meet customer demand. This involves forecasting demand, setting reorder points, and implementing strategies such as just-in-time inventory to minimize inventory costs.
- Manufacturing: A manufacturing company uses inventory management to optimize production schedules and reduce lead times. This involves forecasting demand, managing raw material inventory, and implementing lean manufacturing principles to reduce waste and improve efficiency.
- Hospitality: A hotel uses inventory management to ensure that it has the right amount of supplies on hand to meet guest needs. This involves forecasting demand for items such as towels, linens, and toiletries, and implementing strategies such as par stock levels to minimize inventory holding costs.
Inventory Control:
- Healthcare: A hospital uses inventory control to ensure that it has the right amount of medical supplies on hand to meet patient needs. This involves maintaining accurate inventory records, identifying and addressing discrepancies, and implementing measures to prevent stockouts or overstocking.
- Logistics: A logistics company uses inventory control to ensure that shipments are accurately accounted for and tracked throughout the supply chain. This involves maintaining accurate inventory records, implementing barcode scanning or RFID technology, and implementing strategies such as cross-docking to minimize inventory holding costs.
- Retail: A retail store uses inventory control to prevent theft or loss of inventory. This involves implementing security measures such as surveillance cameras or electronic article surveillance tags, as well as conducting regular inventory audits to identify and address discrepancies.
Conclusion of Inventory Management and Inventory Control
In conclusion, while inventory management and inventory control are related concepts that are used to manage inventory in businesses, there are important differences between Inventory management and Inventory Control.
Inventory management is a broader concept that encompasses all activities related to inventory, including demand forecasting, procurement, storage, inventory tracking, cost analysis, and risk management. It is a long-term, strategic planning process that requires the involvement of various departments such as sales, production, and finance. The goal of inventory management is to optimize inventory levels, minimize costs, and meet customer demand.
On the other hand, inventory control is a more specific activity that focuses on ensuring that inventory is properly counted, tracked, and accounted for. It involves maintaining accurate inventory records, identifying and addressing discrepancies, and implementing measures to prevent stockouts or overstocking. Inventory control is a day-to-day operations process that requires physical inventory counting, record-keeping, discrepancy identification, and inventory replenishment. The goal of inventory control is to maintain accurate inventory records, prevent stockouts, and avoid overstocking.
In summary, effective inventory management requires a combination of strategic planning and day-to-day operations, while effective inventory control requires a focus on accurate inventory tracking and accounting. Both inventory management and inventory control are necessary to optimize inventory levels, minimize costs, and meet customer demand.
References for Inventory Management and Inventory Control
- Difference Between Inventory Management and Inventory control
- https://eswap.global/seven-inventory-management-techniques/#:~:text=Conclusion,%2C%20carrying%2C%20and%20ordering%20costs.